Interest certainly seems to be growing in lift trucks in manufacturing and distribution that are powered by hydrogen fuel cell technology. Coca-Cola for example is running one bottling plant in Georgia entirely on fuel cell powered trucks, using some three dozen vehicles in all. At the MODEX 2012 trade show in Atlanta this week, Air Products announced it was just about the pass the 1000 vehicle mark in terms of the number of lift trucks for which it is supplying hydrogen in the US.
Most of the media coverage about this has been more focused on the truck technology itself, and the refueling process and stations in the distribution center or plant, and generally not so much around the back end infrastructure requirements and options needed for delivering hydrogen gas to the facility. (See Fuel-Cell Powered Lift Trucks Starting to Make an Impact in Distribution Centers.)
Several providers of hydrogen gas were at the MODEX show, and SCDigest had the chance to meet for some time with representatives from Air Products to discuss these back end issues.
First, we learned a lot more about how hydrogen gas is actually produced. While there are a number of ways to create hydrogen gas, the most popular method today is a refinery-type operation in which natural gas (of which the US has an abundant supply for what right now at least are very low prices) is moved through a process in which steam is brought into the chamber with the nat gas and the mixture is moved over a chemical catalyst.
That process breaks out hydrogen molecules from both the natural gas as well as the water/steam.
It turns out there are many uses for that hydrogen besides the fork truck or other fuel cell-based vehicles, which means that there are many generating facilities already across the US. That is important, because as we discuss below, how far a given facility is from such a refinery is a key determinant of the delivered cost of the fuel itself as well what the lowest total cost approach will be.
For example, at a high level, hydrogen can be delivered in gas form in pressurized tanks from which gas is pulled into a facility directly. The other main alternative is to bring the gas tank in liquid form, requiring "cryogenic" storage tanks on site that maintain temperatures hundreds of degrees below zero.
The advantage of the pure gas form is that less equipment is needed at the local DC or factory, costs savings that will ultimately accrue to the company using fuel cell trucks. But the disadvantage is that logistics costs to get the hydrogen to the facility will much higher, since the liquid form delivers quite a bit more energy per pound than the gas form.
So, there will be a system on the outside of a building to store the hydrogen in liquid or gas form, which involved more components if the liquid form is used. For either approach, the output into the building is pure hydrogen gas, which will usually be delivered into as few as a couple of filling stations in the building, or as many as six to eight, depending on the number of vehicles being used and the size of the facility, says Bruce Luff, business development manager at Air Products.
For companies using gas form deliveries, the main component is really a storage area for an array of gas tanks that automatically switch from one tank to another as each is consumed.
For companies using liquid hydrogen, a cryogenic storage tank is needed as mentioned above, then a compressor to convert the liquid into gas that is then stored in high pressure tanks at about 5000 PSI, the level the trucks need for refueling. The gas moves through the compressor to buffer storage and then on to the filling stations through gas lines.
In almost all cases, the hydrogen company manages inventory levels and consumption to ensure the hydrogen is always available to the facility, using an array of technology to support "supplier managed inventory" programs in the same way most industrial gases are handled today.
Luff says that the predominant scenario today and into the future will be companies using the liquid hydrogen approach to reduce logistics costs, though each case is different.
Infrastructure Costs are Amortized Through a Long Term Lease
In most cases, the hydrogen provider will pay for the costs of the outside and inside infrastructure, and then recover those costs as part of a long term lease of 7-10 years. Under that arrangement, they will be responsible for the maintenance of the system as well.
So, that means companies will have to factor in those lease costs in deciding their overall approach. Higher logistics costs for using hydrogen in gas form in some cases may be worth the reduction in lease costs over time because the infrastructure and maintenance costs will be lower.
Also worth considering is that the "density" of hydrogen producing refineries is certain to increase over time. The closer a facility is to a hydrogen facility, the lower its delivery costs will be regardless of which hydrogen form is used. Understanding which provider has or plans to have a refinery nearby can be an dominating factor in deciding which supplier to use. However, larger companies may want to think about this from a total network perspective, rather than one facility at a time.
As for the hydrogen itself, Lutt says the contracts are usually structured so that the price a company pays for a period of time, such as each month, is tied to benchmarks for two input costs: the price of natural gas used in producing the hydrogen, and the cost of diesel needed to ship it. As each goes up and down, the price for the fuel changes.
The good news is that most expect natural gas prices to stay low for years as more and more shale gas sources come on line - with the caveat that many environmental groups are fighting that move over concerns about the "fracking" process used to extract the shale gas.
Was this article helpful? Do you have something to add? Let us know your thoughts atthe Feedback button below.
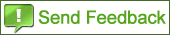 TheGreenSupplyChain.com is now Twittering! Follow us at www.twitter.com/greenscm |