Richard Murphy, CEO of Murphy Warehouse Co., a Minneapolis-based 3PL, died unexpectedly in early July at age 67.
Murphy was very active in CSCMP for many years, serving on the organization’s board for many years, including as board chair.
But SCDigest remembers him best for a great presentation he gave on greening warehouse operations at the 2013 WERC conference.
As SCDigest wrote in our summary of that WERC conference, “This was a simply outstanding presentation on the real math of fluorescent lighting versus LED, turning land around DCs to "prairies" versus cut grass, growing rainwater run-off costs and what to do about it, and lots more. The bottom line message: there is a solid (but not always great) ROI from a wide variety of Green investments in the DC.”
It turned out to be our presentation of the year.
Below you will find our subsequent Green Supply Chain article written shortly after the conference. The numbers may be different today, but the thought process used is as valid as ever:
He and the company have a deep commitment to sustainability in its operations, but also a deep commitment to business success. Can those two imperatives co-exist well together in a third-partly logistics business?
Absolutely, Murphy told a large audience at the Warehouse Education and Research Council (WERC) annual conference in Dallas last week. In a presentation laced with actual detail about costs and payback rarely seen at such events, Murphy walled the audience through a number of case study examples from his company's operations. With almost 3 million square feet of warehouse space under management and 120,000 truck loads managed per year, the company certainly has the scale to gain some real insight into the numbers.
Murphy Warehouse has already made significant progress in sustainability. It has two LEED gold and one LEED silver certified buildings in its Minneapolis campus, and is working towards gold or perhaps even platinum certification for another operation it recently acquired in Eagan, MN.
"LEED certification is not for the faint of heart," Murphy said early in his presentation at WERC.
The company also has ISO 14001 certification for environmental performance and management, expects to achieve a new sustainability certification this year from the International Warehouse Logistics Association.
Murphy then took the audience through a number of specific examples of how the math - meaning the business case - played out for a number of different Green initiatives his company has looked at and usually deployed somewhere in its network.
The company recently acquired an existing 350,000 square-foot DC somewhere in Minnesota, and wanted to change the lighting. An analysis began of the options, resulting in the numbers you see here.
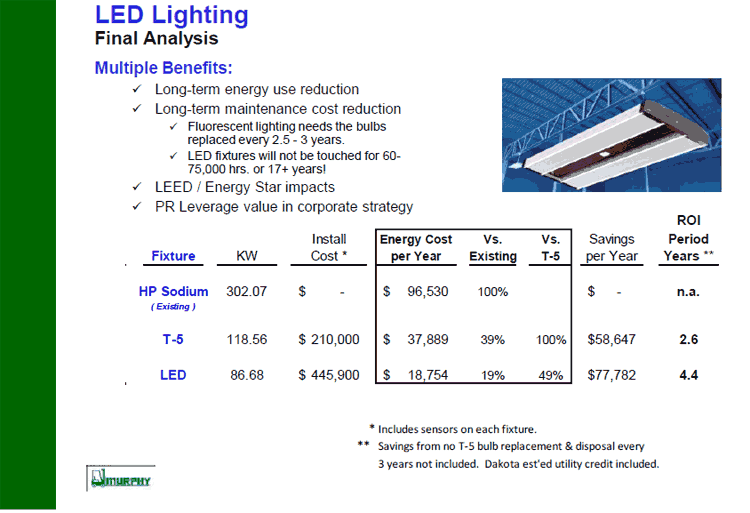
The existing sodium lights cost about $96,000 a year to operate. Fluorescent replacements would cost $210,000 to install (lights, fixtures, installation) but drop the operating expense to just about $38,000 per year.
LED's would cost $446,000 to acquire and install, but drop the annual operating expense to just under $19,000 annually.
The payback period on the right shows the fluorescents have a full financial return in 2.6 years, versus a 4-year period for the LEDs. You could say that math for LEDs does seem to quite add up, and your be right based on just investment and operating costs, but there are still a number of tax and other incentives for investing in LED, reducing the effective cost and the payback period.
Murphy in the end went with the LED solution because he believed it was the right thing to do and it had an acceptable level of payback. Interestingly, he noted that he recently spoke to a friend who worked at a large public company, and in a similar situation that company went with the fluorescents because of the improved payback period.
Murphy also noted it is important to thoroughly evaluate what fixtures you will plan on using for an LED project, saying that companies should begin that evaluation early in the analysis. The good news is that you will usually need fewer fixtures with LED because of their increased light output.
So bright, in fact, that in Murphy's case it discovered after installation that if associates looked up into the LED lights they were often momentarily blinded, leading Murphy to later add diffuse lenses to them. Test a few lights before full installation, Murphy recommended, find any such issues upfront.
The company also added motion detectors to the fixtures that would turn off the LEDs if no one was in the area for a set period of time, and did this on outdoor LED lights as well, where it appeared such detectors were added for the first time to LED fixtures.
Murphy offered many more examples of Green opportunities, including an interesting idea on turning grassy areas around a distribution center into "prairie" areas that use wildflowers or other native plants as an alternative to mowed grass.
Such an approach can be far less expensive to maintain than grass, said Murphy, who it turns out actually has a college degree in landscape architecture. Mowing, fertilizing and watering can add up to big bucks over the course of a year for grassy areas, he said.
At one facility where they have installed prairie plants, it costs the company just $4200 per year in annual maintenance costs for six acres of prairie, versus $21,600 at another DC to maintain just four acres of mowed grass. If all 10 acres were mowed grass, the annual costs would rise to some $52,000, versus less than $10,000 for all prairie - and that winds up being a lot of cash saved.
Murphy said that "Over the last 16 years we have saved over $947,428 while being green by planting native prairies on two logistics campuses."
Murphy added that often when Murphy Warehouse is mentioned in the town where the prairie landscape has been added, the reaction is "Oh, you're the one with the pretty flowers" - a positive image for the company. In fact, the plants are so nice that attempts have been made twice by local thieves to dig up and haul some of them away (once successfully). He counseled, however, that you should not expect such beauty in the first year - wildflowers will take 2-3 years to really develop.
Once established, you have to perform a "burnoff" every three years or so to replicate what typically happens in nature, where a lightning strike usually causes a fire in the wild after the plant growth really builds up. The prairie areas will re-establish themselves on their own after such an event.
Water Runoff Charges are a Growing Problem
Murphy said charges from municipalities for excess water runoff are a major and growing issue. Apparently, a Federal law long on the books for cities to better manage water runoff during major rainstorms is finally being enforced, and the rule says the cities must now do so without assistance from Federal funds - so they are looking to charge to make up the funding gap. More than 2000 cities are now charging businesses (and even households) such fees, and that number is growing - along with the size of the charges.
Murphy said in Minneapolis, for example, the charge is about $3400 per acre. What started as a $58,000 annual fee became a $68,000 fee and then moved over $70,000 each year.
There are a number of options for reducing water runoff, including the prairie strategy discussed above (such plants hold more water than grass), retention ponds, gutter systems that hold and/or slow down the flow of water during a storm, underground piping systems, and more. It is not the total amount of water actually coming off a property that is the concern as much as it is the timing of that release. Just slowing down the flow during a storm can make a big impact of what would be considered excessive runoff.
However, just because a company reduces or slows its water output into a storm system does not necessarily mean the local government will reduce or eliminate the runoff charges. So, the first step is to work with those local agencies to test their general willingness to reduce the fees if water levels could be abated, then investigate various options for doing so, making the investments of course only after securing a firm agreement as to the level the runoff charges will be reduced.
In the case of Murphy Warehouse, the company certainly did want to eliminate or reduce this growing fee, but as usual also "wanted to do the right thing."
In the end, Murphy was able to get a deal with the city of Minneapolis to eliminate 100% of the fee after it would implement a multi-part solution that included a retention pond, new underground piping and storage, and other components. That investment cost $580,000, providing a base return period of 8.5 years. However, with federal tax credits, that number fell to about seven years, and that is without considering that the current fees could rise still higher in coming years.
Murphy went ahead with the project.
Not only have the initiatives discussed here as well as other projects Murphy covered in his presentation provided the company with a strong or at least acceptable business case, they have been a boon to the company from a marketing perspective, Murphy said.
The company has been featured in many article in trade, environmental and business publications (including now SCDigest), won sustainability awards, and has a differentiated value prop for potential customers looking to improve their own sustainability numbers.
"Our investments have been good for the environment, and also very good for Murphy Warehouse Company," Murphy told the audience.
Do you have any thoughts to add on Richard Murphy’s passing? Anyone remember this WERC or similar presentations from Murphy. Let us know your thoughts at the Feedback button below.
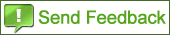
|